Research Underspend – the story of a Green Belt project
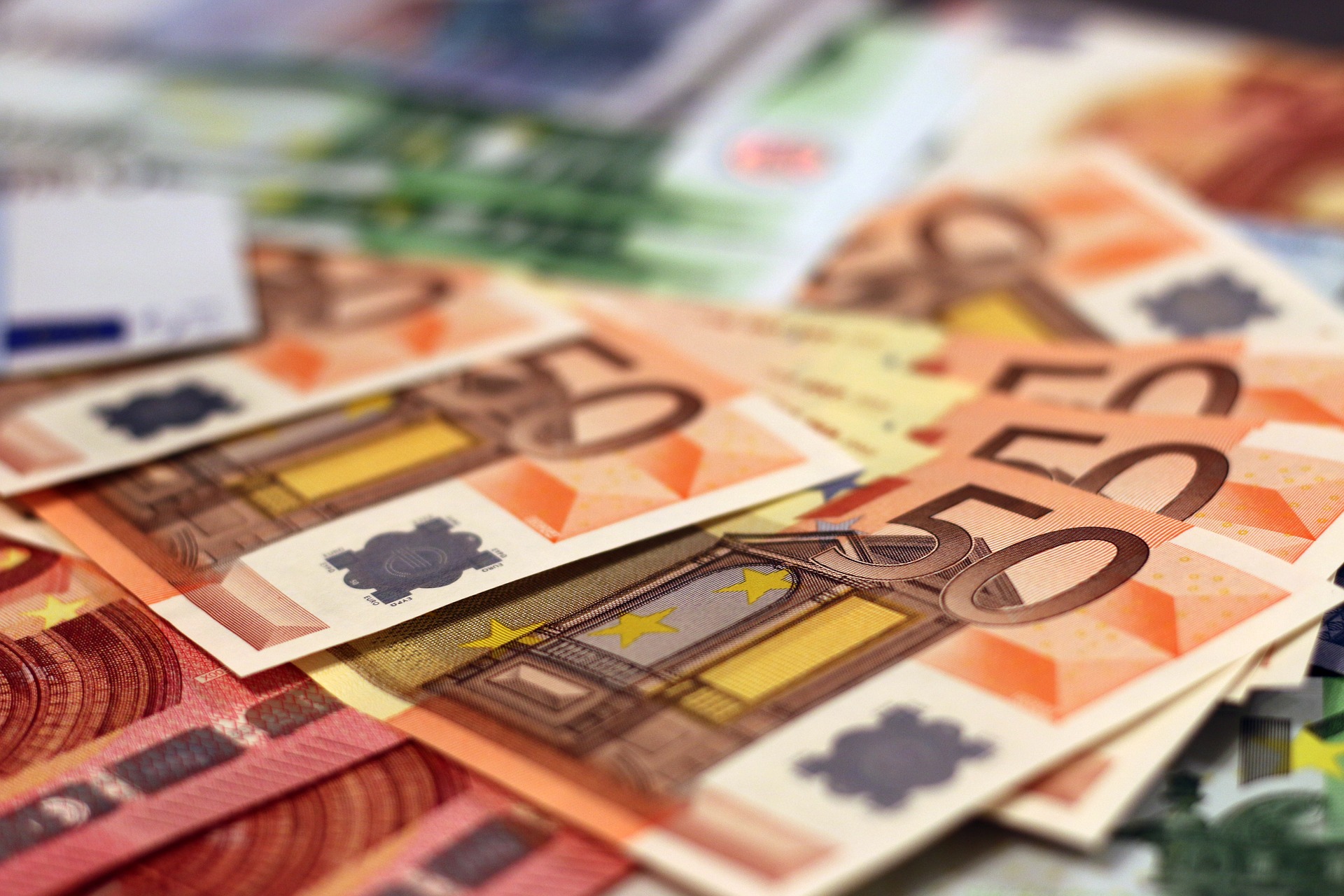
By Michael Sinnott, Director of Agile
As anyone knows who has ever put together a plan to spend money for some good reason or other, there are three ways spending goes – you spend exactly what you planned to spend, you run the risk of spending more, or you underspend. Getting your planning exactly right is a great skill – well done if you manage that. However, while putting the controls in place to prevent over spending is relatively straight forward, it turns out that underspending is the more complex issue.
Why worry about research underspends? Firstly, because the amount that goes into our research overhead is based on what we spend and not what we are awarded – if we underspend we reduce funding for our research infrastructure. Secondly, research metrics, including those used in the various rankings, is one of the metrics used to show what is spent on research so if we underspend it has a negative impact on those metrics. This gives two good reasons to look into research underspends – to help maximise the funding for the research infrastructure and to support our research metrics and rankings.
I met with Stephen Manual recently because he had just been awarded his Green Belt (a 10 credit level 7 award in Process Engineering) and I wanted to recapture the story of his project, drawing on the wisdom of Stephen’s hindsight as he looked back on what they achieved. When they started out – Stephen’s project team was Peter Gallogly, Siobhán Morrissey and Niamh Ryan from his office – they had some ideas on what the cause of underspends might be but the scale of the question was off-putting – the underspend needle in an €80m+ annual haystack. Lean Six Sigma provides the approaches and tools which might help and this meant, for Stephen, a six day training programme, split in three two day sessions in October, November and December 2016, as well as the study and familiarising that goes with becoming confident in any new skill. His team, too, undertook the one day ‘Yellow Belt’ training Agile provides so that, together, they would have a common set of concepts and approaches as they set out to deal with this issue.
The project was not just about finding the answer to the question but was a personal opportunity for Stephen:
“I’m glad I did it. It was an opportunity for me to do something new – the training and the development side. It was the most comprehensive training I have taken part in when in UCD”.
Stephen had experience of complex projects before – the euro conversion project in another Irish third level institution being a good example – and Lean Six Sigma training added a new philosophy and skills..
The project experience
The project was daunting at the start, and not just the question of finding time, in a busy schedule, for the six days’ training. There was also the question of who to bring into the project team, who to involve directly in the project, how to communicate in relation to the project. One of the learnings is that when you take on a large project, especially one with a training element, extra support is needed. It is too easy to end up with a project as well as ‘the day job’.
Lean Six Sigma is great for getting you to run workshops. A key moment which unlocked this project was a workshop which included all the stakeholders and during which, looking at causes and effects, twenty different causes of underspends were identified. One of the issues identified, for example, was the fact that one of the research funding agencies cycle for funding of PhD students was not sequenced with funding calls, giving rise to gaps between funding and available PhDs, delaying project mobilisation and having knock-on effects, including underspend risks, over the life of an award. They used the ‘fishbone diagram’ and ‘cause and effect diagram’ tools to draw ten potential root causes out of the overall picture and these ten then drove the main business of the analysis phase of the project.
You will have guessed by now that this is an analysis project rather than a process enhancement project and so there was quite a bit of data analysis used. This involved digging into some of the ten causes through data, where it was available, and for other areas it was a question of ‘back to the customer’. Stephen and his team surveyed our c. 950 researchers and got a very healthy 28% (265) response rate. One of the key findings from the survey was that the reporting then available was opaque, did not make clear if you were underspending and, if underspending, by how much: the reporting did not provide information that prompted and supporting action. Through working with the researchers a new set of reports has been developed which does these things.
What came from all the work? Stephen:
“We got the answer to our question – there was no single cause but we identified and gave relative weighting to the causes, supported by the data analysis and survey.”
I had met with Stephen just after his Green Belt award had come through, looking for his wisdom of hindsight and some thoughts for others considering one of these larger projects. “I’m glad I did it!” was his first comment, quickly followed by the practicality of
“never underestimate the time commitment – it will be more than you think”.
Many of us engage with projects in our own areas so the following was particularly interesting –
“You should not make assumptions as they have the power to influence your conclusions, to steer you, and you need an open mind if you really want to get to the heart of the issue you are addressing”.
Stephen used the ideas and techniques of Lean Six Sigma to open minds, dig into causes, analyse data, listen to customers, come up with some immediate solutions… all part of his finding the answers to the question “Why do research underspends happen?”